Boston Dynamics has released a new video showcasing its Atlas robot. This machine, once famous for its parkour skills and backflips, is now doing something very different. Atlas is hard at work sorting parts in a factory. This marks a significant change for the robot. It is moving from being a show-off to a useful tool in real-world environments.
From Parkour to Practicality: Atlas’ New Mission
Not long ago, Atlas was the star of viral videos. It performed parkour stunts and flipped mid-air effortlessly. However, this new chapter for the robot shows a shift. It’s moving from flashy moves to practical tasks that could change how we work.
In Boston Dynamics’ latest video, Atlas is seen in a factory setting. It is no longer just showing off. Now, it’s learning how to pick up parts from narrow racks. This task helps improve its dexterity and allows Atlas to familiarize itself with the environment. The company claims the robot’s real value lies in its ability to perform practical tasks in the real world.
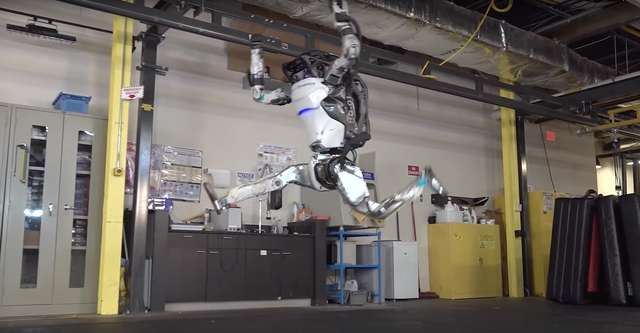
Boston Dynamics’ Vision for Atlas
Robert Playter, CEO of Boston Dynamics, explains the vision behind the project. The collaboration with the RAI Institute brings together two leading organizations in robotics. Their goal is to accelerate Atlas’s core capabilities. They aim to establish the robot as a valuable asset in everyday life.
A year ago, Boston Dynamics unveiled a new version of Atlas. This iteration is faster, stronger, more compact, and neater than ever before. It has been designed to take on a variety of tasks. Boston Dynamics believes it will revolutionize how we work. The company has broken down big goals into smaller, manageable problems to drive progress.
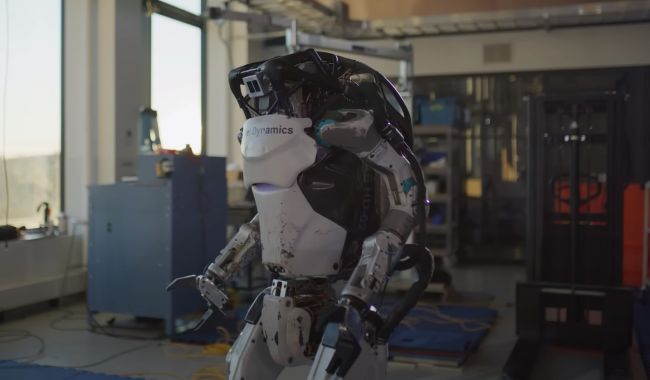
Atlas: A New Task for Manufacturing
Recently, Boston Dynamics identified Atlas’s first custom task: sorting parts in a factory. This shift marks a key moment in Atlas’s journey. The robot is now entering the world of manufacturing. In this industry, robots can provide real-world utility.
What Is Parts Sorting?
Parts sorting is a common logistics task in factories, especially in automotive manufacturing. On production lines, different vehicle models and configurations are assembled. Workers must prepare the correct parts in the right order for each car. Sorting is the preprocessing step where parts are arranged according to the car being assembled that day.
Thousands of parts arrive at the factory in bulk. They are stored in single-SKU containers, each containing only one type of part. Workers retrieve the parts and place them in the correct order for the assembly line.
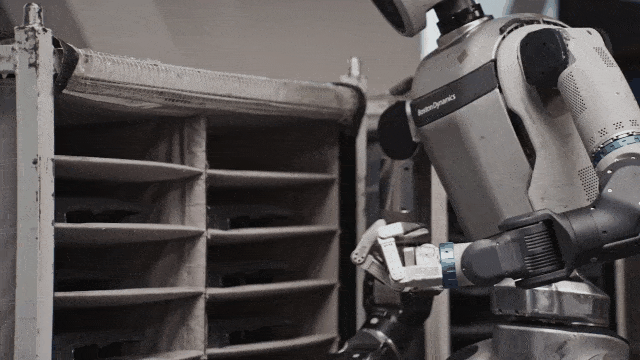
In one test, Atlas is shown sorting engine hoods into a rack. These parts are then placed beside the assembly line for workers to pick and install them in cars.
Parts Sorting: A Challenge Worth Tackling
Parts sorting presents several core challenges that are crucial for humanoid robots. Unlike traditional automation, humanoid robots like Atlas are designed to adapt to a variety of tasks. A complete solution for parts sorting involves Atlas handling thousands of different parts. It must also perform various pick-and-place tasks.
These parts differ in size, shape, and weight. This requires Atlas to handle them in a way that minimizes mistakes and maximizes efficiency. This is where the integration of reinforcement learning and foundational models come in. These tools help Atlas improve its performance by creating a robust system that can learn and adapt.
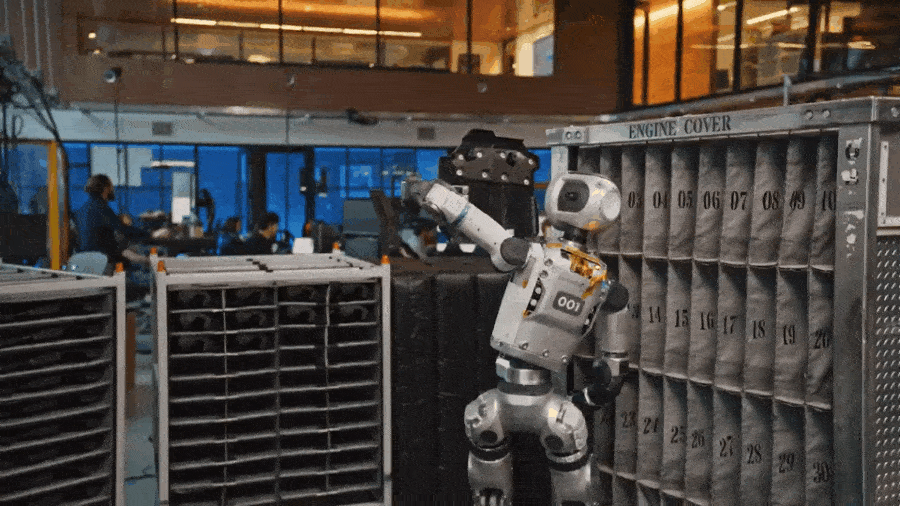
The Complexity of Parts Sorting
Parts sorting is not a simple task. It involves multiple steps that require high reliability. Atlas needs to understand how parts can go wrong during the picking, handling, and placing stages. It also needs to recognize when something’s off and figure out how to correct it.
If robots require human intervention for every minor error, or if they frequently damage parts, they lose their value. Therefore, Boston Dynamics has invested heavily in creating systems that allow Atlas to complete complex tasks without constant oversight.
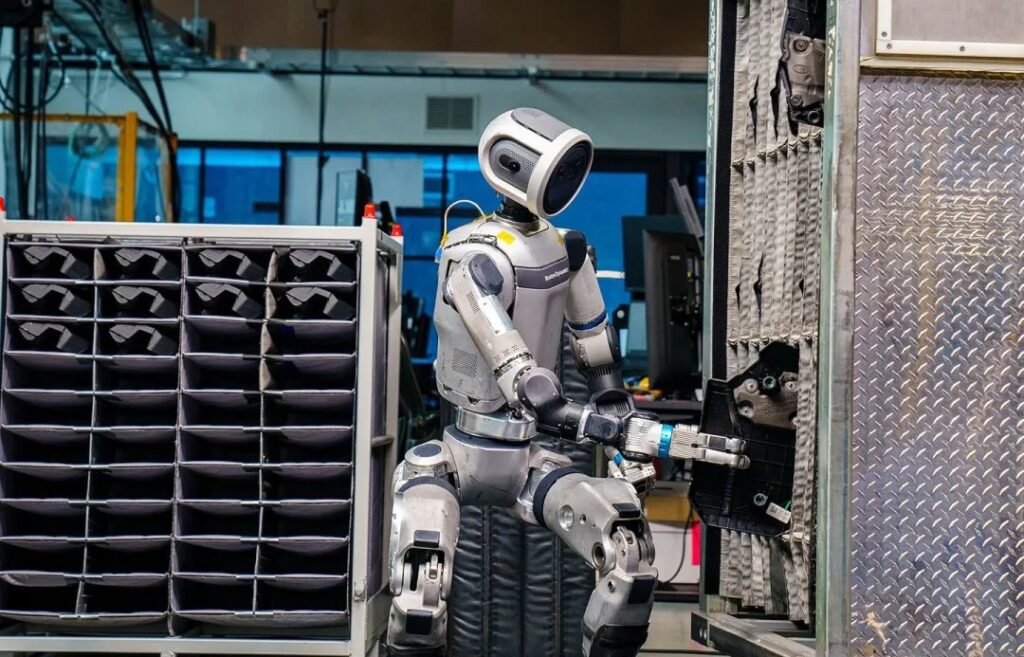
Why It Matters
Parts sorting is challenging, but it’s also a task that could greatly improve productivity in manufacturing. By automating repetitive actions like bending, lifting, and twisting heavy components, Atlas reduces the risk of human injury. It also boosts employee retention by eliminating the most physically taxing aspects of the job.
Humanoid robots like Atlas are uniquely suited for such tasks. They can easily integrate into existing workflows and adapt to changing environments—just like humans.
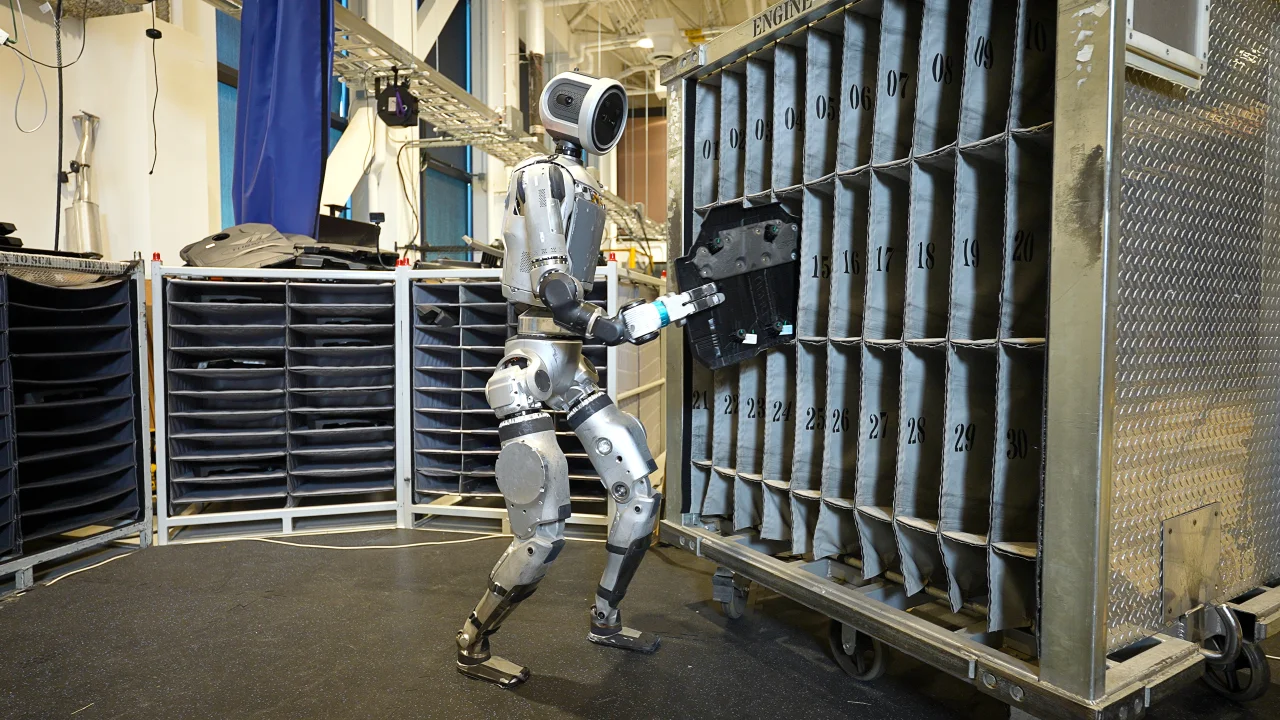
The Road Ahead
Looking ahead, Boston Dynamics is rapidly scaling Atlas’s capabilities. The robot has already been tested in modern factories. The company plans to expand its use with pilot clients to refine and innovate its functions. They believe the widespread adoption of autonomous robots will mirror other revolutionary technologies that have reshaped our lives.
Conclusion
Atlas’s transition from parkour to practical manufacturing tasks signals a new era for robotics. While challenges remain, the potential for humanoid robots to seamlessly integrate into human-centric environments could lead to a future. In this future, robots like Atlas will play a crucial role in improving efficiency, safety, and productivity across industries.